働き方改革の影響を受けて、業務改善に取り組む企業が多くあります。業務改善を行うことにより生産性向上が期待できることから、自社でも取り組みたいと考える経営者や管理者もいるでしょう。しかし、業務改善にはさまざまな手法があり、やり方によっては失敗に終わるケースもあるため注意が必要です。
そこでこの記事では、業務改善で有名な「トヨタ式」の内容を踏まえつつ、業務のムダ削減について・業務改善を行う際の流れについて紹介します。作業の効率化やワークフローの見直しを進めたい経営者・管理者の人はぜひ参考にしてください。
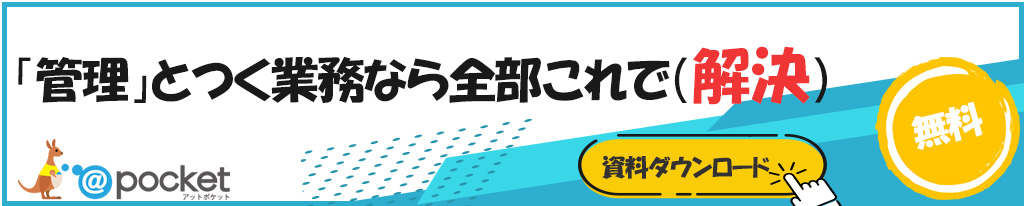
目次
業務改善とは?
業務改善とは、商品やサービスを生み出すために必要な資源のムラ・ムリ・ムダを省き、企業の利益や従業員の働きやすさの向上を図ることです。業務改善の、ムラ・ムリ・ムダは、以下のような状態を指します。
ムラ | 業務を処理する時間が、人によってバラバラである状態 |
ムリ | 人員に対して、業務量が多すぎる状態 |
ムダ | マニュアル確認など、必要のない業務に時間が割かれている状態 |
ムラ・ムリ・ムダが蔓延した状態では、モノ・ヒト・カネなど、必要な資源が無駄遣いされているため、企業にとっては不利益です。
そのため、意識的に業務改善策を練り、ムラ・ムリ・ムダを削減する取り組みが必要です。
業務削減・経費削減との違い
業務改善と似たような言葉に「業務削減」と「経費削減」があり、以下のように定義できます。
経費削減は、光熱費・備品・人件費など、発生している経費を削減することを意味します。
たとえば業務削減によって社員の残業時間が減れば、光熱費や人件費がコストカットできるため、経費削減に繋がります。
ムラ・ムリ・ムダを省くことが目的である「業務改善」は、「削減」という手段だけでなく、人員配置や業務フローの見直しなど、削減以外の手段もある点がポイントです。
業務改善を行うなら「トヨタ式」|7つのムダの削減
業務改善を進める際は、トヨタ式(トヨタ生産方式)の考え方が役立ちます。トヨタ式とは、トヨタ自動車株式会社が製造過程におけるムダを排除し、現場の作業効率と生産性向上を実現するために編み出した生産方式です。
トヨタ式では、「7つのムダの削除」を基本理念に掲げています。トヨタ式における「7つのムダ」とは、以下のような内容です。
加工のムダ | 「従来からの継続」などの理由によって、本当に必要かどうかの検証を怠ったまま、続けられている作業のこと |
在庫のムダ | すぐに使用する予定のない、不要な材料や部品、仕掛品や完成品を抱えること |
造りすぎのムダ | 納期まで期間がある状態にもかかわらず、必要以上に生産すること |
手待ちのムダ | 「前工程の完成を待っている」などの理由から、付加価値を生み出さない状態のこと |
動作のムダ | 業務中における「探す」「調べる」などの付加価値を生み出さない動作のこと |
運搬のムダ | 必要以上に物を移動させたり、積み替えたりすること |
不良・手直しのムダ | 良品の作り直しやキズの手直しなど、不要な作業をすること |
つのムダの中で、「造りすぎのムダ」は「在庫のムダ」「運搬のムダ」など、新たなムダの原因になるため、特に悪いムダといわれています。
7つのムダは製造業で活用することが一般的ですが、解釈を変えることで異業種へ応用することが可能です。
たとえば「動作のムダ」は、製造業界であればスパナなどの工具を探す時間、IT業界では必要なフォルダーを探す時間、などと当てはめられます。
7つのムダの削減を進める際は、2本の柱に据えられた「ジャストインタイム」「自働化」を意識することが大切です。以下では、「ジャストインタイム」「自動化」の考え方の概要を解説します。
トヨタ式の柱(1)ジャストインタイム
ジャストインタイムとは、必要なときに必要なモノを必要な分のみ生産する仕組みです。ジャストインタイムを深く理解するためには、以下で紹介する「後工程引取方式」「工程の流れ化」「タクト調整」について理解する必要があります。
必要生産数に合わせて部品を引き取ることです。前工程では後工程から依頼を受けた量のみ生産するため、「在庫のムダ」を削減できます。
必要以上の生産を避けることで「造りすぎのムダ」も抑制でき、必要なモノを必要な分のみ生み出す体制を実現することが可能です。
一つの製品が手直しなどで、前工程に戻ることなく次工程にスムーズに流れる生産状況のことです。「不良・手直しのムダ」「運搬のムダ」などを削減することができます。
タクト調整とは、製品一つを生産するためにかかる時間を調整することをさします。なお、製品一つを生産するためにかかる時間のことをタクトタイムと呼びます。
工程の流れ化を止めないためには、前工程でかかる生産時間と次工程でかかるタクトタイムを把握し、タクト調整を行う必要があります。
ジャストインタイムを活用するためには、最初にタスク一つあたりにかかる時間を把握する必要があります。次にタスクのチェックや修正にかかる時間の削減に取り組むことが大切です。
最後に、必要なタスクを必要なだけ割り振ることができる状況を作ると良いでしょう。また、ジャストインタイムを活用するためには、必要な人材の育成も欠かせません。
トヨタ式の柱(2)自働化
自働化とは、異常を感知したときに自動的に機械が止まり、人間によるチェックを受ける仕組みを作ることです。機械が自動的に止まる仕組みがあるからこそ、人間による監視の労力を最小限に抑え、効率的な生産体制を実現できます。
トヨタ式における「自働化」は、人偏(にんべん)のない「自動化」とは全く異なる概念です。人偏のない「自動化」・トヨタ式における「自働化」の違いは、以下の表を参照ください。

トヨタ式の自働化では、異常が発生すると検知する仕組みであるため、不良品の発生を最小限に抑えることができます。結果として、不良・手直しのムダを削減するとともに従業員の負担軽減に繋げることが可能です。
自働化によって、必要最低限の従業員で足りる生産体制が実現できるため、コスト削減にも繋がります。
業務改善を行う際の流れ
正しく業務改善をするためには、大まかな流れをあらかじめ把握し、ステップ別に進めることが大切です。大まかな流れを頭に入れておかなければ、「取り組みの成果が分からない」「作業者の負担が増加した」などの事態を招くリスクがあります。
業務改善を行う際の大まかな流れは、以下のような内容です。
(1)業務を可視化し、正しく現状を把握する
(2)把握した現状をもとに、問題点を列挙する
(3)問題点の中から、改善ポイントを洗い出す
(4)業務改善計画を作成する
(5)業務改善を実行する
(6)業務改善の実行結果を評価する
(7)新しい業務改善計画を作成する
業務改善の効果検証では、以下のようにQCDに着目する方法がおすすめです。
Q:Quality | 商品やサービスの品質向上目的の取り組みを評価する指標 |
C:Cost | 商品やサービスを作り出すための必要コストを測定する指標 |
D:Delivery | 商品やサービスの提供までにかかる時間を評価する指標 |
QCDのバランスがとれて、従業員の満足度が高い状態になることが理想のゴールといえるでしょう。効果検証をした結果、「修正が必要」と判断した内容は、新たに業務改善を行う際に活かします。課題点の洗い出しや現状把握、目標の作成を繰り返し、企業の変革に繋げてください。
業務改善にはシステム導入がおすすめ
業務改善に向けた事前準備では、現在の業務を可視化して、正しく現状把握をすることが大切です。そして正しい現状把握を行うためには、システムがあった方が便利です。
ここでいうシステム導入とは、情報をためる受け皿作りと情報を共有する仕組みを作るものです。数々の業務の問題を記録し、どの業務を改善すべきかを特定する。そして実際に業務の改善まで雄子合う、そのためには情報の蓄積と共有が必要です。
今現在、そのような情報共有の仕組みが無い場合は、ぜひシステムの検討も行ってください。
まとめ
この記事では、業務改善の意味と手順、成功に繋げるためのポイントを解説しました。業務改善とは、商品やサービスを作り出す際のムラ・ムリ・ムダを省き、企業および従業員の利益を創出することです。
業務改善を効率的に進めるためには、システムの導入を検討しましょう。情報の蓄積や共有といったところが進むと、業務においても共有体制が整うため、業務改善が進めやすくなります。
最後に、弊社サービスの@pocket(アットポケット)は、プログラミング不要で現場で業務アプリを作れるシステムです。情報の蓄積や共有といったところでも十分活用いただけますので、ご興味がありましたら、ぜひ30日間無料トライアルを触ってみてください。
その他、各企業様に合わせた導入・運用のサポートをしていますので、システムを使った業務改善に興味がある方は、ぜひお気軽にご相談ください。
業務削減は、業務改善でいう「ムダ」の削減にあたり、今ある業務そのものを削減することを意味します。
社員一人ひとりの業務を見直し、適切な業務削減を行うことで、社員の負担を軽減するだけでなく、他の重要な業務にリソースを充てることが可能です。